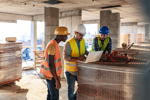
Upskilling and training project professionals in Engineering Construction industry is key to meeting demand increase
Association for Project Management (APM) is highlighting the need for the increased recruitment and upskilling of project professionals in the engineering construction industry (ECI) to address the rising demands and growing skills gap in the industry.