When does quality need to be managed?
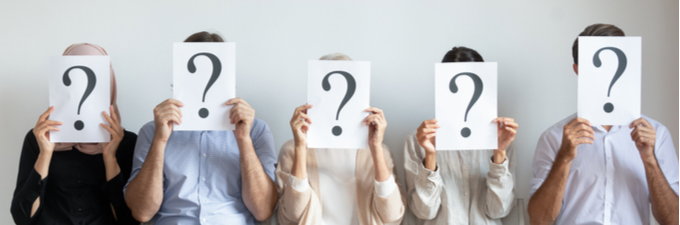
Quality needs to be managed throughout the complete project life cycle. That means quality management must begin right at the start of the project to be really effective. The more thought put into fitness for purpose and acceptance of the solution early in the project, the better the chances of its success.
The evolving scope of quality management
Quality thinking has evolved and quality activities have started progressively earlier. The oldest quality method, inspection, occurs late in the project life cycle. When faults are found, it is too late to prevent redesign and rework with their attendant costs and delays. Lean thinking starts quality involvement at project inception and expands the breadth of quality thinking from products through processes to people and culture – the human resources, and their value system and behaviours. This is because anything less usually causes major rework and delays towards the end of the project. The diagram below (adapted from Project Success and Quality: Balancing the Iron Triangle) shows the evolution of the different methods in stage and scope.
As mentioned, inspection occurs late in the work, and rework later on can be catastrophic and the cost of scrapped or waste components found by inspection can be substantial. Achieving 100 per cent confidence is rarely economic either, as the inspection process is time consuming and expensive in effort.
Quality control builds on inspection, expanding the focus from the products to the processes that produce them. The quality control approach remains focused on detecting cases where quality standards have not been met.
- This is still an expensive way of tackling quality due to waste and rework; and
- the risk of undetected quality issues reaching the end of process/supply chain is significant, as are the consequences.
Quality assurance was the next development, aiming to prevent problems rather than just curing them by focusing on ‘baking in’ quality. This starts right at the planning and design stage for each product. The sorts of activities required to shift from cure to prevention include:
- creating and applying a suitable quality management system that aims to deliver conformance to requirements;
- quality planning from the start, ideally applying systems thinking disciplines to ensure the problem is fully understood and scoped;
- applying systems engineering disciplines to produce a design which is ‘fit for purpose’ and fully solves the problem;
- designing each product/process to avoid defects; and
- training and motivating staff to avoid defects.
Quality assurance still has its limitations, as there is a quality ethos in project delivery without the same ethos in project sponsorship and governance. This gap in thinking disappears in Lean.
Lean (originally incorporating Total Quality Management) builds further on quality assurance, extending quality management to all aspects of the organisation, its customers, its suppliers and its key business processes. Lean is a philosophy of continuously developing products/services, methods and processes ahead of competitors.
It's vital to start at the beginning
Understand the requirements and acceptance criteria
It is important to be very clear what the project is trying to achieve from the start. This is defined by two elements:
- What the project must deliver (especially the outcomes it will support, not just the products it will deliver)
- The acceptance criteria for the project as a whole
Completion of most projects requires the delivery of many products, including documents, physical items and services. Each of these needs validated requirements and acceptance criteria to ensure the project can succeed.
Agreeing and documenting acceptance criteria early in the project helps to clarify any uncertainty when there is still time to address it. If acceptance criteria are not defined with the requirements, they may be left until acceptance is due; when thinking them through reveals flaws in the original requirements.
Consider the Scottish Parliament building which had an aspirational aim of being "the visual embodiment of exciting constitutional change". This is subjective and cannot be tested – it is unsuitable as a measure of success. Acceptance criteria must be testable. Defining the acceptance methods and acceptance plan in parallel to the acceptance criteria themselves ensures that the criteria specified can be tested and confirmed.
NHS Direct had clearly thought through its requirements for a new website and how it would measure success before placing the contract with its suppliers. This enabled me as project lead to steer the project to a very successful outcome with no significant rework, delivering on time and budget, with only minor changes to scope. The NHS reported a 1000 per cent return on investment in the first year alone and we won four awards.
Make a project quality plan
Fail to plan, plan to fail.
Quality planning starts early, but its ramifications extend to the very end of the project i.e. acceptance and shutdown (and probably even further - operations and decommissioning).
The first important output of quality planning is the project quality plan. This lays out how quality will be managed throughout the project to achieve the quality outcomes and objectives required, including:
- Roles and responsibilities
- Planning, reporting and recording of quality activities
- Standards, tools and techniques, plus auditing, to be used
It needs to define how all the quality management systems in the supply chain (customer and suppliers), will integrate and operate together.
The project quality plan needs to flex in response to changing situations throughout the project, under rigorous change control, as any change to the quality plans ultimately links back to project success.
Request and review the supplier’s quality plan
Each supplier needs to provide a quality plan for the products they are supplying, appropriate to the complexity and risk associated with those products.
At its very simplest, the supply of non-safety-critical wood screws for use in an office environment would not require a distinct quality plan. However the supplier’s quality plan for a major component (replacement boiler, aircraft engine) may be as comprehensive and detailed as the quality plan for the entire project.
Quality is a major consideration in selecting suppliers for a successful project. Request a draft quality plan as part of the tender process to achieve these advantages:
- Quality is explicitly included in supplier selection and risk assessment.
- The prospective supplier understands how the project operates.
- An otherwise viable supplier with poor quality management can be rejected.
Delivering success starts at the beginning of the project with good planning, which needs to include good quality planning. In the next blog I’ll explore further the key elements of quality management through the life cycle.
Further reading:
- Project Success and Quality: Balancing the Iron Triangle
- Who delivers quality in a project?
- What is quality management and control?
Image: fizkes
0 comments
Log in to post a comment, or create an account if you don't have one already.