What will make delivering quality easier, boosting project success?
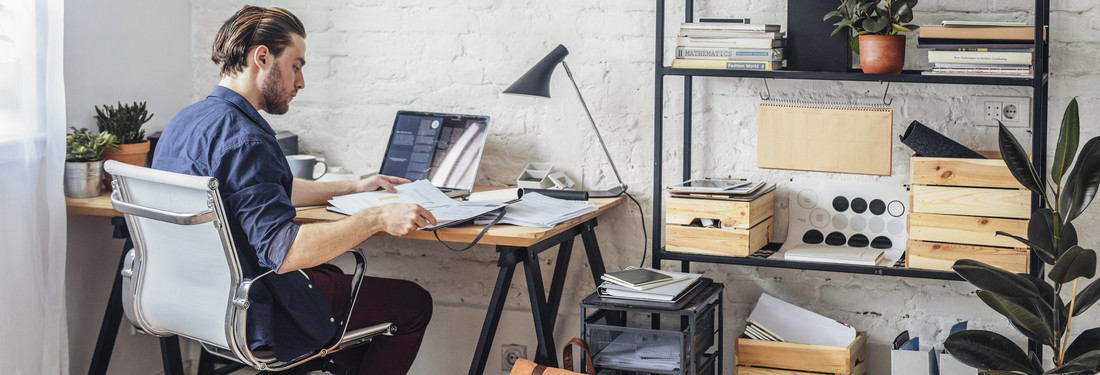
Project quality management is complicated, which explains the number of projects suffering from poor quality, and my previous blogs broke it down to simpler elements to discuss separately.
- What quality means in the project context and why its good management cuts delays, waste and over-spend and disappointed customers
- Everyone involved in the project is responsible for quality which demands both the culture and communications s to underpin it
- Quality needs to be managed from the very start of the project through into operation
- True requirements (not specifications) are the basis for quality
- ‘Left-shifting’ quality planning prevents projects going down rabbit holes
- How you can manage quality down the supply chain effectively
The most recent looked at how agile approaches could improve quality through improving understanding of true requirements, focusing on fitness-for-purpose.
People are a critical part of the ‘project system’ and must feel motivated to make it work. For example, many estimating systems suffer from the ‘GIGO’ principle i.e. garbage in, garbage out – because collecting precise data is both tedious and time-consuming, and since there is no obvious benefit to the folks who have to collect and log that data, they don’t bother. Here’s how to bring all these different elements together to deliver quality and achieve project success.
Building a quality culture
How do we motivate everyone in the project to have a quality focus? It’s not trivial. My student summer jobs were both working in quality control for manufacturers, and both made it very clear the financial impact of poor quality in the product, and the vital importance of collecting accurate data. When I joined a major UK computer manufacturer and they ran a corporate quality improvement programme, I was sold already. What was disappointing was that many longer-serving staff just shrugged it off as ‘yet another initiative’. I learned then that a corporate culture change wasn’t realistic – a project leader must rely on creating a quality culture within the project themselves. This means educating team members about quality management and explaining the cost and schedule implications of poor quality.
Quality management as a means of delivering success, not meaningless bureaucracy
It also means ensuring that quality plans and quality activities are not seen as compliance with some corporate standard, but are focused on delivering a successful outcome, i.e. deliverables are fit for purpose and deliver the benefits expected. Most people skimp on bureaucracy they find meaningless but are motivated to collect clearly beneficial information accurately. After teaching quality to a cohort of mature students, one of them reported that he’d put his £100M+ project on hold for three weeks to make all their paperwork coherent, focused on the desired outcome. He was confident this would avoid many future problems, but the ‘tick box’ culture had allowed incoherent documentation to be approved at the previous stage gate.
Engaging all stakeholders
Good quality management has to deliver benefits that are obvious to everyone involved in doing it, not just quality specialists. This means addressing the needs of a diverse group of stakeholders, including:
- quality planners
- project managers
- project controls team
- testers, quality auditors and acceptance signatories
- sponsors (including programme and portfolio managers)
- suppliers down the supply chain.
Supply chain quality
There are several common problems with supply chain quality, ranging from poor internal communication between the supplier’s sales force and their supply team to counterfeiting. Most supply chain quality issues can be reduced or even eliminated by providing all supplier direct access to the definitive requirements and specifications relevant to them. This avoids misunderstandings and working to out-of-date versions of specifications and drawings.
Automation to make it all easy
Finally, let’s make the mechanics of quality management as easy as possible. For this, automation is essential and expected – we are well into the 21st century, and have an app for everything else. Success in introducing automation into project quality management requires that it’s clearly seen to make it easier for everyone.
In conclusion
The reward of good project quality management? The project delivers a solution that is fit for purpose, minimising the delays and cost increases from rework and remediation i.e. success.
Modern technology can help by automating quality tasks, but simply adding yet another IT system cannot solve the problem. There are some point IT solutions that address part of this problem already. To be transformative, the technology must solve the whole problem through integrating all aspects (and existing systems), supported by the motivation of all stakeholders to use it effectively.
The critical themes in quality management boosting project success are:
- One project, one team, one success – across commercial and contractual boundaries; the project leader needs to talk the talk and walk the walk
- Quality management activities need to be easier for everyone, from sponsor to end user - a fully integrated IT solution avoiding rekeying of data and making accurate information capture as quick and easy as possible
- Making quality-related communication throughout the supply chain much easier and completely transparent – sharing ‘one truth’ by secure technology - no confusion, no version errors, no misunderstandings
- Showing the hard cash benefits of good quality management to justify the front-end investment in excellent quality planning
I’ve been pulling together 30 years of professional experience with insights from the organisations collaborating over the last two years. The result so far is a comprehensive set of requirements for a solution to the whole quality management challenge, and a high-level system design. Next step? Develop a proof-of-concept solution and pilot it.
Anyone interested in collaborating on this, get in touch via the contact section of the Systems Thinking SIG page.
You may also be interested in:
1 comments
Log in to post a comment, or create an account if you don't have one already.
Thanks Andrew - this is a really interesting article. Thinking about the complex programme I am working on at the moment it strikes me that one of the challenges to quality management is the sheer variety the systems engineering programmes generate. I really like the idea of keep quality focused on requirements, not specifications. Engagement with the customer, up front, to understand how a requirement will be accepted...and what is really important about delivering that requirement can really help to focus the project team on what matters from a quality perspective. I guess the trick is achieving this effectively across a huge requirement set that includes both functional and non-functional requirements.